THE CHALLENGE
Due to a number of reports involving civilians driving their cars into retail store entrances and crash & grab crimes in Northern California, a big box retailer with 25 properties in the area made a proactive decision to install security bollards in front of its entrances before any damage was done. The installation of bollards in retail applications has risen sharply since the 1995 Oklahoma City bombing and the 9/ 11 attacks. Placing bollards in the vicinity of a property is a practical way of protecting property, personnel and customers without detracting from a retailer’s carefully crafted brand image.
THE SOLUTION
Because of Divisions’ boots on the ground in the area and our success with the management of the retailer’s exterior maintenance services across the country, Divisions was selected to coordinate the bollard installations. Beginning with an extensive site survey process, our field team captured detailed photographs of each property, and coordinated third party inspections to locate underground utilities or water lines prior to breaking ground. With a solid understanding of each property’s scope of work, geographical and timing requirements, Divisions could begin the process of securing the best service providers for the work. Because of the precision that goes into bollard selection, placement, and installation, the service provider must have the right combination of expertise, special equipment and manpower to execute 25 locations against a 30 day time frame – while also confining work to morning hours to limit interruptions to the retailer’s profitable business hours.
For proper installation, a bollard’s weight is carefully balanced with the depth and location of the hole. Once digging for bollard placement had begun, Divisions was on site to monitor that measurements were being retaken at key intervals in order to ensure successful completion. Divisions was also responsible for communicating project progress with each municipality and coordinating review visits with safety inspectors. Insufficient communication with city officials could lead to potential work stoppage and ultimately derail the tight schedule.
Throughout the project Divisions also communicated with our customer’s corporate team to keep them abreast of the progress. Photographs were posted online daily for review, and at project completion, Divisions walked each property to perform a final inspection and photograph the completed work.
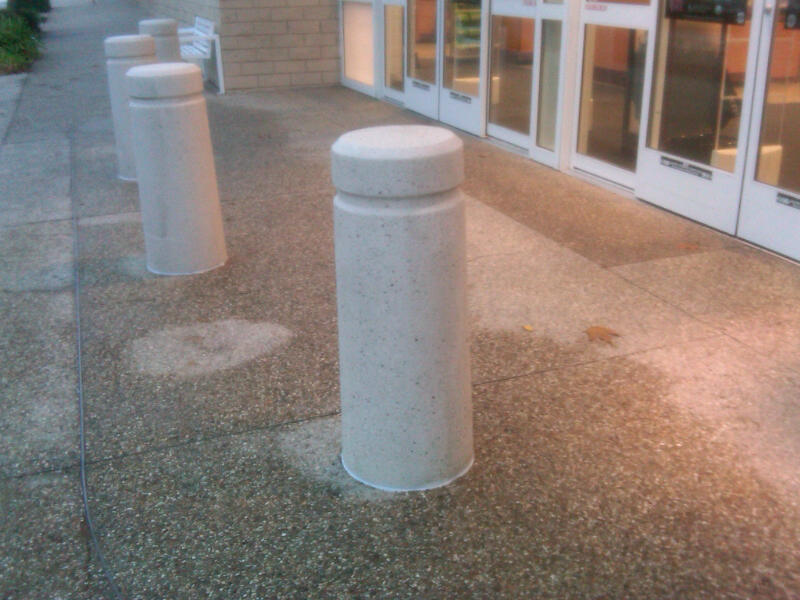